Lors de leur entrevue, Valerio Frediana, Industry Technology Strategist chez Microsoft et Koen Groothaert, VP Operational Excellence chez Bekaert arrivent à la conclusion que la combinaison d’une fine couche MES et de la plate-forme numérique flexible de Microsoft constitue la bonne recette pour accélérer tout le processus de numérisation de Bekaert.
Vu que Valerio travaille avec de nombreux clients industriels sur leurs stratégies de transformation numérique et leurs feuilles de route, il siège dans plusieurs comités de pilotage.
Pour les non-initiés, un comité de pilotage est l’occasion de se réunir et de prendre le pouls de l’exécution de la stratégie avec ses clients. Cela revient à évaluer l’état des initiatives les plus pertinentes, s’attaquer aux problèmes critiques ou aux obstacles et se réjouir à la perspective de relever les prochains défis en tant que partenaires.
Les meilleurs d’entre eux sont l’occasion d’évaluer les résultats positifs d’initiatives qui se sont multipliées et se sont développées au cours des derniers mois – voire même, des dernières années. Valerio pense plus particulièrement à un exemple récent avec un client qui se tient fort à cœur : Bekaert. Bekaert est une entreprise belge fondée il y a 140 ans. Il s’agit du plus grand producteur indépendant au monde de produits en fil d’acier, avec environ 28.000 employés et 5 milliards d’euros de chiffre d’affaires annuel.
Lors de leur dernier comité de pilotage, ils ont passé en revue un projet intitulé « Digital Way of Working » – fruit de 18 mois de collaboration.
Il était à ce point ravi et excité après cette réunion avec Bekaert qu’il a décidé que ce serait un sujet intéressant pour cet article. Et fort heureusement, Koen Groothaert – VP Operational Excellence chez Bekaert – a accepté de partager avec lui quelques réflexions sur cette aventure.
“Le projet Digital Way of Working s’avère pertinent pour la plupart des entreprises manufacturières, car elles ont la possibilité de renforcer leur efficacité en usine en mettant en œuvre une stratégie d’applications de fabrication intelligentes grâce à une combinaison d’outils de collaboration de type low-code et par ailleurs, standard basé sur le cloud.”
Au cours de leur discussion, ils ont parlé des ambitions du projet et de l’effet extraordinaire qu’il a déjà dans les usines de Bekaert. Voici quelques-uns des extraits les plus intéressants.

Le début : de la normalisation à la numérisation avec MES
Valerio : Alors, commençons par décrire le contexte. Quand Bekaert s’est-elle engagée dans la voie de la transformation numérique ?
Koen : Notre transformation numérique a commencé dans notre division de renforcement du caoutchouc – composée d’environ 20 usines. Il y a cinq ans, nous avons lancé deux programmes importants.
“Il est capital de comprendre que, lorsque vous souhaitez numériser des composantes du processus de fabrication, il est primordial dans un premier temps de les standardiser – pour ainsi disposer d’un modèle global.”
Le premier programme était le « Bekaert Manufacturing System » (BMS). Le but de BMS était de disposer d’un système et d’un mode de travail normalisés et uniques dans chacune de nos usines – ce qui nous permettrait ensuite de réaliser un changement radical dans la performance opérationnelle.
Une fois le BMS opérationnel, nous avons lancé le deuxième programme – le Manufacturing Execution System (MES). L’objectif du MES était d’introduire une traçabilité complète des matières premières aux produits finis, tout en enregistrant toutes sortes de manifestations dans l’atelier de fabrication, comme par exemple, des épisodes de qualité ou des événements provoquant des arrêts de machines, ainsi que la direction de certains processus, comme nos véhicules à guidage laser, etc.
Donc, en termes simples : BMS concernait la normalisation, MES concernait la numérisation.
Valerio : Je suis plutôt curieux d’en apprendre plus sur vos expériences avec le programme MES. Je suis convaincu qu’un MES est fondamental à la numérisation des opérations de base. Toutefois, je n’ai jamais rencontré un programme sans faille.
J’ai expliqué dans un article précédent que j’étais persuadé que la combinaison de défis technologiques et méthodologiques ainsi qu’une approche de mise en œuvre lente sapent véritablement la valeur potentielle de tels programmes. Quelle est votre expérience ?
Koen : Eh bien tout d’abord, le déploiement de notre MES s’est fait plutôt lentement. Nous l’avons implémenté dans moins de la moitié de nos usines sur une période de cinq à six ans. Nous avons donc connu une courbe d’apprentissage assez longue.
De plus, du fait que l’approche est assez centralisée, vous ne pouvez pas permettre à de nombreuses équipes différentes de travailler sur un système MES ou de développer des fonctionnalités en même temps.
En outre, nous sommes une entreprise avec un grand nombre de machines, et avec le MES, il s’agit en effet de connecter chacune d’entre elles. C’est donc un gros investissement et cela ne se prête pas à une intervention rapide.
La naissance du « Digital Way of Working »
Koen : Après un certain temps, nous disposions de beaucoup de données via le MES, mais il n’a pas été facile d’extraire toutes les données du système et de vraiment les transformer en informations exploitables que les opérateurs ou les superviseurs de l’atelier pouvaient utiliser.
C’est la raison pour laquelle nous avons finalement lancé la prochaine phase du BMS, à savoir, « Digital Way of Working ».
Valerio : Super. Pouvez-vous nous en dire en plus à ce sujet ?
Koen : Bien sûr. Il y a environ 18 mois, nous avons décidé de rechercher une technologie qui pourrait nous aider à transformer nos données en informations exploitables, et qui en même temps, permettrait une approche « glocale » pour s’éloigner d’un système 100% centralisé tout en disposant toujours d’une gouvernance centrale.
Nous souhaitions une solution évolutive. Nous avons donc convenu d’examiner trois usines différentes, dans différentes unités commerciales, dans différentes régions – et même avec des dorsales informatiques différentes.
Nous avons visité ces usines pour travailler avec les employés et les inspirer. Nous leur avons montré des technologies et des capacités de pointe, et nous avons réfléchi ensemble en vue d’identifier les opportunités de numérisation axée sur la valeur. Des aspects tels que l’augmentation de la disponibilité de nos machines, la gestion du flux de travail, l’aide aux opérateurs dans la gestion de leurs tâches, la sécurité, une meilleure collaboration, etc.
À ce stade, nous n’avions pas encore sélectionné d’outil ou de technologie. Une fois les besoins identifiés, il nous fallait définir l’architecture de la solution, puis sélectionner un partenaire qui nous fournirait la technologie requise.
Valerio : Effectivement. C’est donc là que nos routes se sont croisées. Lorsque nous avons entendu parler de ce que vous tentiez de résoudre, nous avons immédiatement pensé que la mise en place d’une stratégie « low-code » en plus des outils de collaboration standard aurait été suffisamment flexible pour réduire les barrières à l’adoption, mais suffisamment standard pour permettre un déploiement rapide. Notre idée était de vous donner une certaine liberté pour la personnalisation locale tout en gardant une gouvernance globale et un déploiement rapide, itératif et agile des fonctionnalités.
Et pour être honnête, Koen, nous sommes plutôt fiers de cette implémentation. C’est ce que nous appelons en interne : un « parcours à trois clouds » complet, ce qui signifie le Cloud de Productivité avec Office 365, les Applications d’Entreprise avec Dynamics 365 et la Plate-forme Cloud avec Azure. Plus précisément, nous avons utilisé Microsoft Teams pour encapsuler PowerPlatform et plusieurs autres outils de collaboration Office 365 tels que Planner et Forms – tous pris en charge par Azure DevOps et plusieurs services Azure PaaS (Platform-as-a-Service).

Koen : Eh bien, c’est la raison pour laquelle nous avons opté pour Microsoft. Nous sommes vraiment satisfaits de l’ensemble de la coopération jusqu’à présent, de la phase de l’architecture de la solution mais aussi tout au long de la livraison.
“Et je suis vraiment persuadé que cette combinaison d’une fine couche MES et de cette plate-forme numérique flexible de Microsoft est la bonne recette pour accélérer tout le processus de numérisation de Bekaert.”
En plus, nous avons maintenu les utilisateurs finaux fortement impliqués tout au long du processus, comme vous le savez. Et le premier feed-back de tous les superviseurs et opérateurs est particulièrement positif.
L’effet sur les ateliers de fabrication
Valerio : Alors, pouvez-vous expliquer ce qu’a signifié le projet « Digital Way of Working » pour les gens de vos ateliers de fabrication ?
Koen : Absolument. Dans la plupart des cas jusqu’à présent, l’accent a été mis sur l’augmentation du temps de disponibilité et un rendement accru des ressources existantes. Pour ce faire, il est très important de fournir des informations au superviseur en montrant comment le quart précédent s’est comporté. Et aussi pour montrer les performances réelles au sein de l’usine.

Nous avons donc doté tous les superviseurs de tablettes, elles-mêmes munies d’une application appelée « My Shop Floor ». Cette appli leur montre le statut en temps réel de tout, ainsi qu’un rapport de renseignements. Le superviseur peut ainsi voir immédiatement la première chose à faire, et se concentrer là-dessus.
L’un des principaux objectifs de l’ensemble du projet est de raccourcir le temps de réaction face à des problèmes.
Nous nous concentrons également sur la collaboration. Ainsi, lorsque nous avons visité ces trois usines au début du programme, nous avons remarqué que beaucoup d’opérateurs s’organisaient pour communiquer entre eux pendant le quart de travail.
“Pour ce faire, beaucoup d’entre eux avaient créé des groupes WhatsApp. Nous avons donc développé quelques outils de collaboration à l’aide de Microsoft Teams.”
Et un autre domaine important est la maintenance. Nous avons conçu un système de gestion des actions intégré et agile, ce qui signifie que les techniciens de maintenance n’ont plus besoin de se rendre sur un ordinateur de bureau pour ouvrir une note ou réagir à une notification – ils peuvent désormais faire tout cela sur une tablette, ce qui leur fait gagner énormément de temps.
Valerio : Nous avons également parlé de la numérisation de plusieurs outils « lean » tels que « Gemba Walks » ou « Performance Dialogues ». Vous aviez autrefois des outils analogiques, pouvez-vous me dire comment s’est opéré le changement ?
Koen : Oui, nous avons numérisé de nombreux outils « lean ». Par exemple, Gemba Walks, les gens peuvent immédiatement aller avec leur application mobile dans l’atelier de fabrication, prendre des photos, créer des actions immédiatement. Ils n’ont donc pas besoin de retourner à leur bureau par la suite pour rédiger un rapport ou créer des actions. Cela peut être fait tout de suite sans aucune administration supplémentaire.
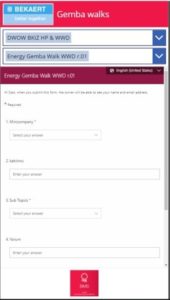
Nous avons également des applications similaires pour les inspections et la gestion des actions – qui font en fait partie des principales applications que nous ayons développées.
Valerio : C’est formidable – des fonctionnalités vraiment cool. Et si on se place du point de vue de l’opérateur, il doit concentrer son attention et filtrer le « bruit ». Disposer d’une application qui dit clairement « Voici le point le plus important, veuillez y réagir » – c’est en soi une fonctionnalité du tonnerre !
Koen : Oui, en effet. Je pense vraiment que BMS Digital nous simplifie la vie, réduit l’administration, etc.
“La numérisation réduit le stress dans l’atelier de fabrication. La technologie filtre tout le bruit des choses qui fonctionnent bien, tout en mettant en évidence les choses qui nécessitent l’attention.”
Valerio : Absolument. Et tout commence avec les gens. C’est une des leçons que j’ai tirées des précédents projets d’implémentation MES : si vous ne concevez pas le système avec les utilisateurs finaux à l’esprit, le résultat se résume à un rejet du système et le programme est un désastre.
Koen : Eh bien, nous avons eu une résistance franchement faible. Les gens l’apprécient. Ils font savoir que c’est très intuitif et exactement ce qu’il leur manquait dans le passé.
De plus, la jeune génération d’opérateurs s’est toujours révélée plus digitalisée à domicile qu’au travail. Du coup, travailler pour nous devient plus attractif à leurs yeux. Ce qui est également une chose très importante pour l’entreprise à l’avenir.